The history of the Hero products
1960's
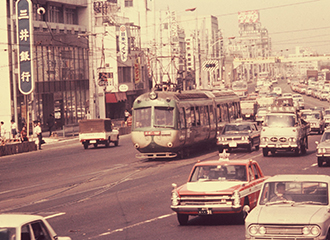

The Japan's high economic growth and doubled personal income caused full-scale motorization. The domestic number of automobiles owned reached the level of 10 million in 1967.
Founder of Hero Electric Kenji Seki recognized the crimping technique using terminals of AMP Incorporated, now TE Connectivity, a globally engaged U.S. connection device manufacturer, benefitting from having been a school friend of one of executives of its Japanese subsidiary, and commenced operation in Sotokanda, Chiyoda-ku, Tokyo, striving to create a new market of professional quality products in the automotive repair field where demand had been predicted to increase.

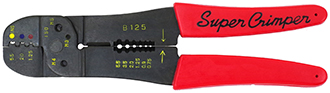
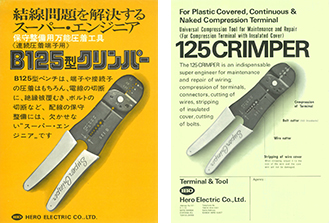
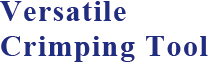
Commitment to professional use
CRIMPER B-125 (Item # B-14), a crimping tool which combines reliability and robustness in itself and became synonymous with an automotive wiring repair tool at the dawn of Japan's motorization
Its excellent durability obtained from the stable structure that sufficiently endures many years of use in field maintenance and our commitment to Made in Japan from designing through manufacturing in order to meet requirements from professionals aiming at perfect maintenance has been highly regarded up to the present date after half a century.
Photo:
CRIMPER B-125 (Item # B-14), a crimping tool which has kept its professional quality for half a century (above)
Leaflets at the time of founding targeting domestic market (below left) and overseas market (below right)
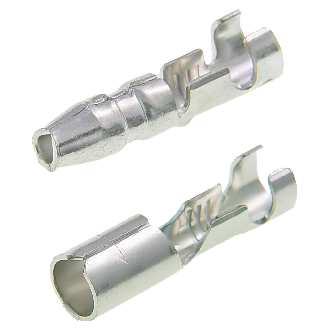

Focus on materials and finishing treatments
Bullet terminals B-1 / B-2, which epitomize Hero Quality obtained from uncompromised commitment in every aspect of materials and finishing treatments in order to meet high level requirements from professionals
Specifically developed for automotive repair parts, our high performance bullet terminals only achievable through uncompromised commitment to Made in Japan and In-house Manufacturing to keep the quality enduring the harsh environment of vehicles boast of its long-term sales success of half a century mainly in the auto aftermarket both in Japan and abroad.
Reasons why Hero's bullet terminals are chosen
Photo:
Bullet terminals B-1 (above) and B-2 (below)
1970's
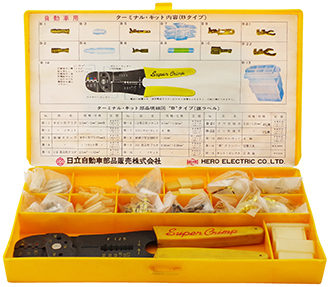

Basic items in a kit
AUTOMOTIVE TERMINAL KIT Type B, professional use, which is carried easily and makes it possible to troubleshoot wiring problems instantly through reliable crimping work, which was developed by challenging to the tradition of standard automotive wiring repair method: soldering. You can perform repairing work regardless of location condition and power supply availability.
Photo:
AUTOMOTIVE TERMINAL KIT Type B
Through the nation-wide sales network established by Hitachi Automobile Appliances Sales Co., Ltd. (now Hitachi Astemo Aftermarket Japan, Ltd.), we have dedicated to spreading products mainly in the auto aftermarket and contributed to improving working efficiency of many professionals.
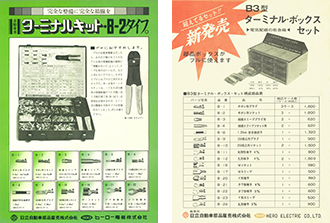
Photo:
A leaflet of a TERMINAL KIT (left)
A sales copy used on this advertising leaflet was Perfect Connections for Perfect Maintenance.
A leaflet of a TERMINAL BOX SET (right)
The Industry's first TERMINAL BOX was commercialized with a nickname of Wiring First Aid Kit
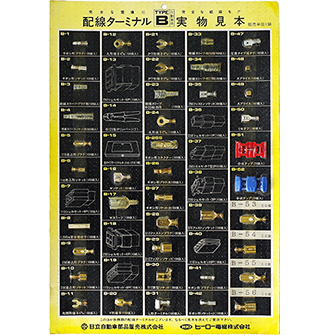
Photo:
AUTOMOTIVE WIRING TERMINAL TYPE-B REFERENCE GUIDE
A Must-Have guide sheet illustrated by pictures, which has been highly regarded by many professionals
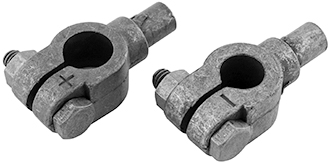

Established a new category
Hero's first crimp type battery terminals DC series, which were newly commercialized in response to high demands from professionals aiming at perfect maintenance
We newly developed a crimp type battery terminal under the inherited basic principle of automotive repair wiring terminal: "Perfect Connections for Perfect Maintenance" which established a new category in automotive repair ahead of the industry.
Photo:
Battery terminals DC series
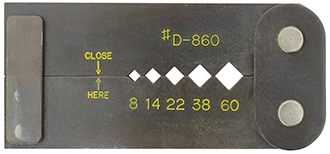
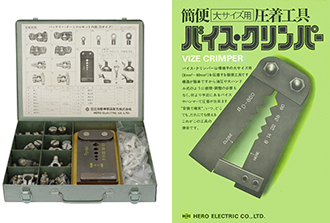
Combined cost benefit with usefulness
Crimping tool # D-860, which combined cost performance with improved field maintenance efficiency
Standard crimping devices for crimp type battery terminals or ring terminals had been expensive hydraulic crimping tools and heavyweight handle-type crimping tools. To replace these tools, we developed a Hero original crimping tool which combined cost benefit and workability. The industry's first automotive repair BATTERY TERMINAL KIT Type D was also newly commercialized.
Photo:
Crimping tool # D-860 (above)
BATTERY TERMINAL KIT Type D (left)
A leaflet at the time (right)
1980's
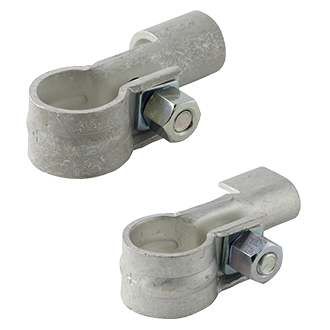
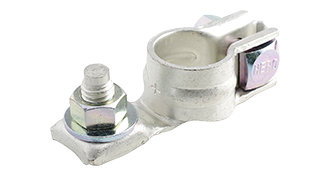
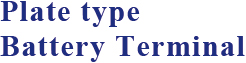
Industry's first material and original forming technology
Plate type Battery Terminal series which combine high conductivity given by its material and robustness enduring professional use in order to pursue further efficiency in power supply
In an age when materials for battery terminals were mainly zinc and zinc alloy, we independently developed the repair industry's first Plate type Battery Terminals, which was made using oxygen-free copper with an excellent conductivity, tackling a new proposition of improving conductivity we had received many requests from professionals.
Photo:
DCPL/DCPS series (above)
DOPL/DOPS series (middle)
DTPL/DTPS series (below)
To provide professional quality products, we have pursued a high performance and reliability of the product itself by committing to Made in Japan and In-house Manufacturing thoroughly from designing to manufacturing.
1990's
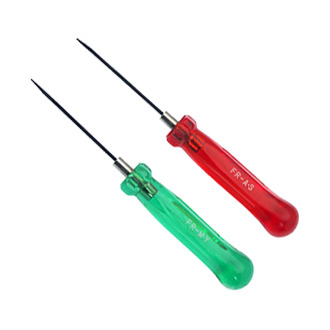
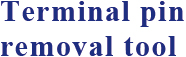
Standard field maintenance tool come from user point of view
Terminal pin removal tool FR-150, which makes it possible to remove various terminals with a single item come from the needs of improving field working efficiency.
One of our original products which was developed based on the experience cultivated for a quarter of a century as an automotive repair parts manufacturer made it possible to remove terminals more smoothly and securely by using so strong material that can be used in aircraft for its shaft and a unique tip form contrived from long years of experience.
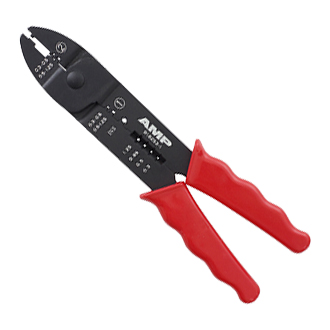
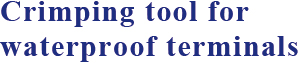
Commercialization led by insights into future marketplace
Crimping tool for waterproof terminals FRC-100, which we have developed ahead of the industry driven by expectations of automotive waterproof connectors to be widespread
The fundamental concept of product development was the same with that of B-14: commitment to professional use. Although its development faced difficulty with an additional challenge of crimping waterproof terminals not seen in conventional concept, we overcome many hurdles and finally succeeded in commercializing the industry's first crimping tool for waterproof terminals.
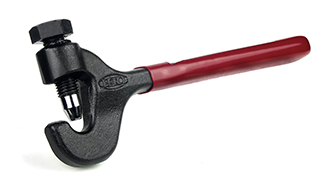

Unrivalled overwhelming originality
Simple crimping tool D-19N, which overturned the conventional crimping methods with an aim to improve efficiency in crimping work in tight spaces
One of Hero's original products born from unprecedented ideas unbound to conventional concepts of crimping tool by going back to the origin of Hero products' consistent principle: Improvement in field maintenance efficiency.
2000's
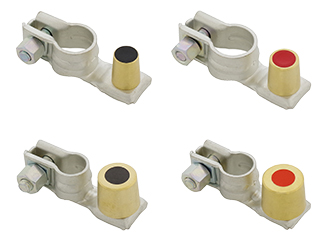
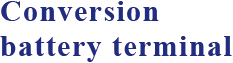
Realization of "I wish such a product existed"
Conversion battery terminal DXL and DXS series, which have generated new needs by putting together our original techniques and expertise in every aspect
To respond a latent needs in battery exchange, we developed this with all our heart passing on long-term in-house experience of designing and manufacturing of automotive repair parts for professional use and the DNA cultivated through the development of the Plate type Battery Terminal.
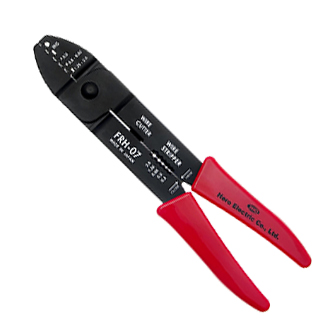
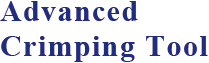
Further enhanced usability and quality
Crimping tool FRH-07, which makes a new history of Hero products passing on the blood of B-14, which had been the premier tool of professional use for half a century, and our waterproof-terminal crimping expertise cultivated through the development of FRC-100
In view of the increased use of finer wiring with electronization of vehicles and increased number of waterproof connectors, we developed FRH-07 with various expertise accumulated through the development of B-14 and FRC-100. Its tooth shape delicately designed with Hero's distinctive approach, which is unrivalled in crimping tools for professional use, realized a beautiful and secure crimping finish of terminals.
2010's
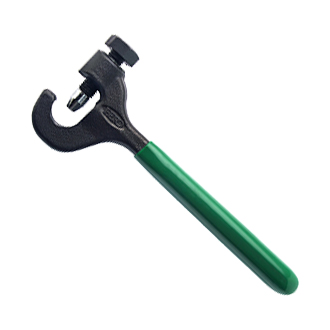
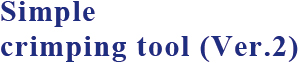
Devised products lead many variations
Simple crimping tool D-20N, which was born as a new model derived from D-19N in response to high demands for commercialization from the market
One of Hero's original products which reflected the terminal crimping technique and a property of tensile strength made it possible to crimp thick wires (38mm2 to 60mm2) to respond many requests we had received.
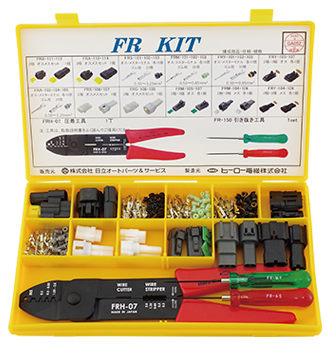
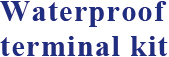
Promoter of pioneering a new field
The industry's first waterproof terminal kit FR KIT, which contains waterproof terminals and Hero original tools, passing on the blood of AUTOMOTIVE TERMINAL KIT Type B,
The industry's first kit specified for waterproof terminals meeting requirements from professionals, which contains various selected waterproof terminals and waterproof housings frequently used in field maintenance, including a crimping tool for waterproof terminals FRH-07 and terminal removal tools FR-150, which uses nickel-chrome-molybdenum steel, one of strongest alloy metals with excellent mechanical property that is used for aircraft parts, as its shaft material, aims to generate new demands
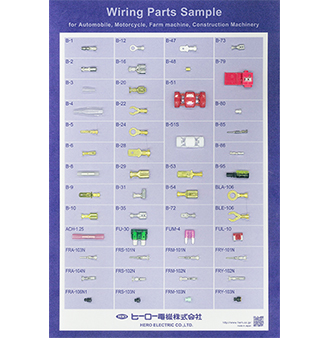
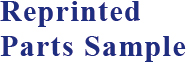
In all ages, a picture is worth a thousand words
WIRING PARTS SAMPLE, a sample board which was modernized the WIRING TERMINAL REFERENCE GUIDE born in response to the needs of the times and achieved a large population for half a century
Based on the industry's first AUTOMOTIVE WIRING TERMINAL TYPE-B REFERENCE GUIDE, which had been highly regarded as a must-have item of maintenance factories to improve automotive wiring repair work, selected representative products (49 items) were contained in a modernized reprinted version.
Hero Electric's bullet terminals B-1/B-2
Reason why these are chosen by professionals for half a century
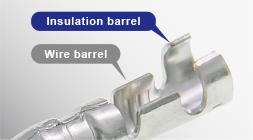
The insulation barrel of our bullet terminals is applied a treatment called pre-form. The most important point when crimping the insulation barrel is to press the wire insulation equally. The form of our insulation barrel treated the pre-form allows the barrel to be set steadily on teeth of the tool to form a good crimped shape as applied pressure.
Products without pre-form are likely to cause crimp defects when crimped abruptly. Therefore, such products require a trick before crimping such as thinning the barrel width or bending the barrel
tips a little bit, resulting in additional processes.
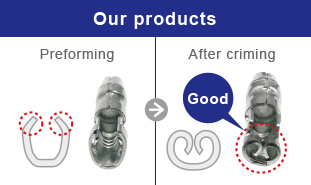
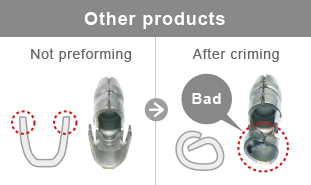