Professional quality bullet terminals for automotive repair
Bullet terminal series for automotive repair
B-1/B-2, B-1-24K/B-2-24K
↓ How to Crimp Wire Bullet Terminals
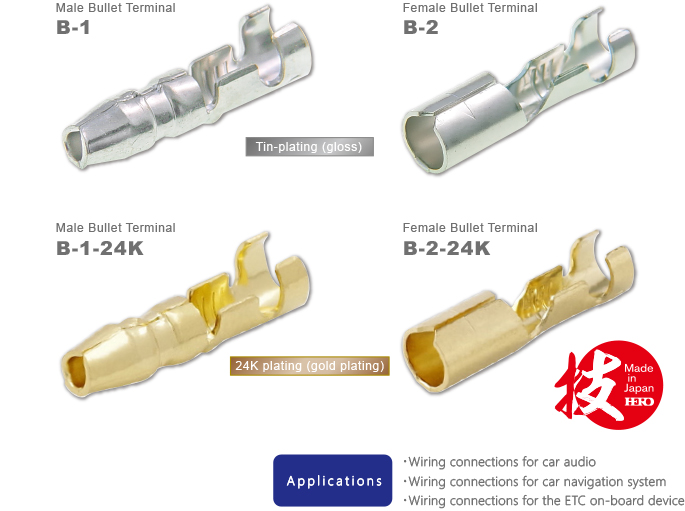
Remarkable point 1
Proof of safety & confidence: "MADE IN JAPAN". This product has been sold for 50 years mainly in the automobile repair parts market both in Japan and overseas.
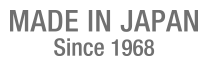
Remarkable point 2
For our bullet terminal, we have developed the product only for automobile repair parts to improve the work efficiency which is required for automobile maintenance. This is a professional use model that reflects our years of experience we have cultivated as a comprehensive manufacturer of crimp wiring terminals only for automobile repair parts.
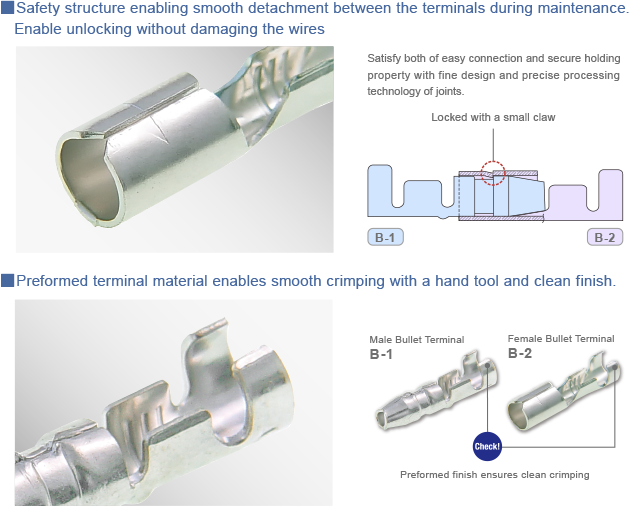
Why Hero Electric "B-1" "B-2" can gain "trust" and "support" from
professional mechanics ?
When you crimp electric wire to a terminal with a hand tool, you can preform the terminal to reduce the slope of the terminal, which is a weakness of the hand tool. This allows “light” and “secure” crimping, realizing reduced working time and a good finish.
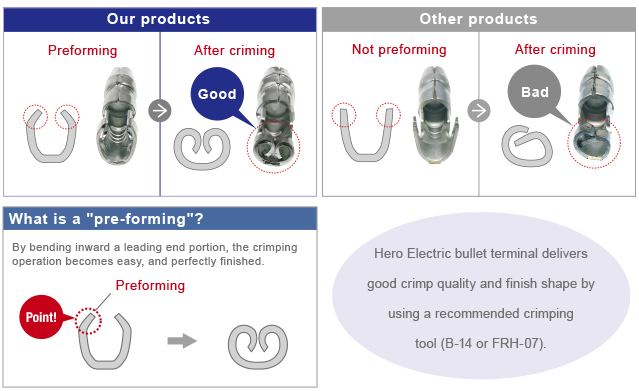
Remarkable point 3
Since this is a professional use product assuming its use by professional mechanics, we have pursued conductivity as a concept from the product development stage. Paying attention to "material", "thickness" and "surface area", we have secured high conductivity.
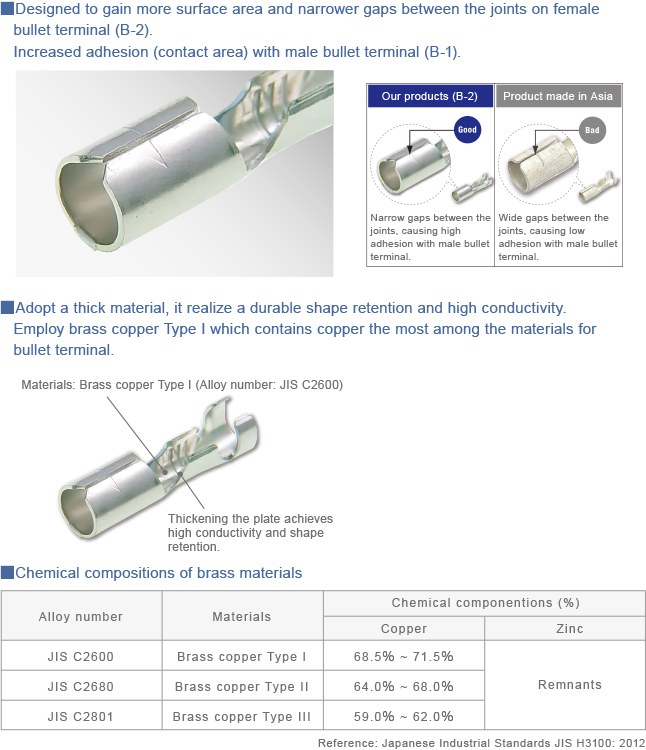
Remarkable point 4
Since this is a professional use product, we have thoroughly paid attention to surface plating to pursue quality to every detail. Conduct tin plating (shiny) or 24K plating (gold plating) after product press to apply plating treatment not only to the product surface but also to the cut plane, which helps to prevent corrosion of the product itself and to reduce conductivity.
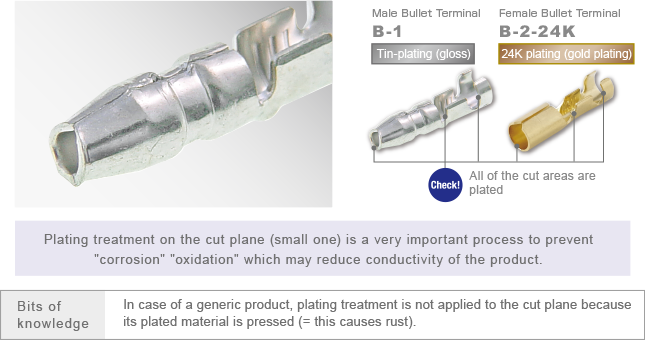
Beneficial advice for crimping bullet terminals
A crimping tool used for crimping terminals, as well as preform/non-preform of the product itself, has a significant effect on the good finish of bullet terminal crimping. Hero Electric crimping tool (B-14 and FRH-07) delivers smooth and reliable crimping by buffing the tooth form which influences the crimp performance.
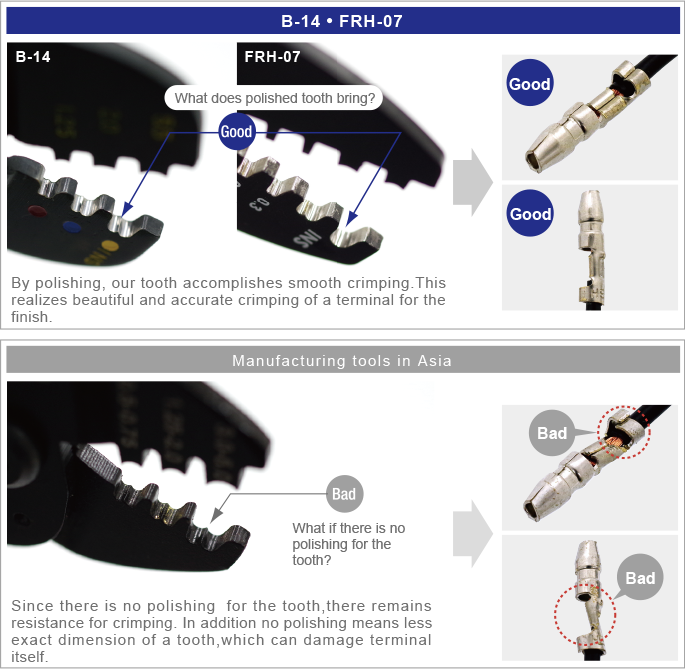
Product name | Male Bullet Terminal | Female Bullet Terminal |
---|---|---|
Product | ![]() |
![]() |
Parts number | B-1 | B-2 |
Alloy number | JIS C2600 | |
Material | Brass copper Type I | |
Surface finish | Tin-plating (gloss) | |
Applicable wire size |
0.50mm2 - 2.00mm2 | |
Application tool |
B-14, FRH-07 |
Product name | Male Bullet Terminal | Female Bullet Terminal |
---|---|---|
Product | ![]() |
![]() |
Parts number | B-1-24K | B-2-24K |
Alloy number | JIS C2600 | |
Material | Brass copper Type I | |
Surface finish | 24K plating (gold plating) | |
Applicable wire size |
0.50mm2 - 2.00mm2 | |
Application tool |
B-14, FRH-07 |
How to Crimp Wire Bullet Terminals in an Easy-to-Understand Way
In the past, wire bullet terminals and crimping tools were for professional use, but nowadays they are increasingly being used by the general public.
Crimping a wire bullet terminal requires proper knowledge and skills. Incomplete crimping can lead to poor contact and broken wires.
That's why Hero Electric has prepared this manual with the concept of "making it easy for anyone to understand".
This time, the male bullet terminal (Part No. B-1) is used as an example.
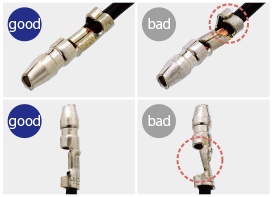
Step 1 : Preparing the product
There are two types of Hero Electric crimping tools that can crimp bullet terminals: FRH-07 and B-14. The FRH-07 is used here.
FRH-07
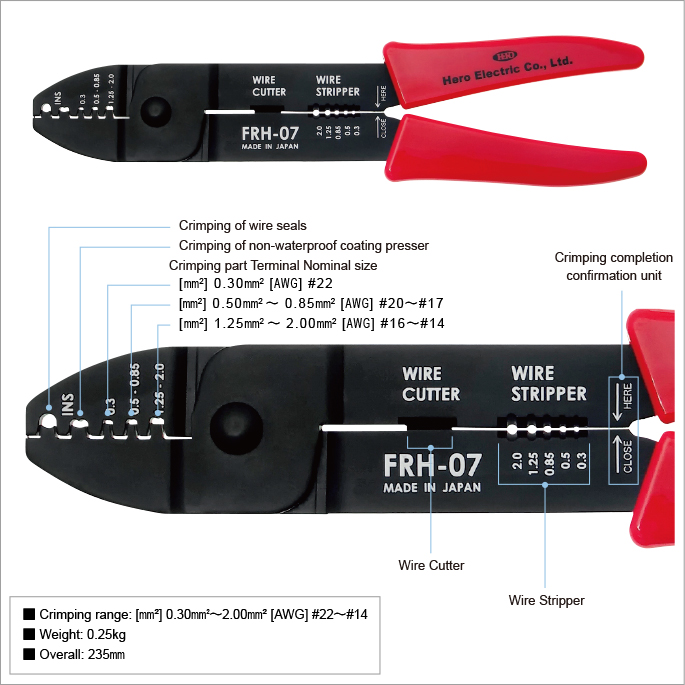
Compatible product
![]() |
![]() |
![]() |
![]() |
![]() |
![]() |
Male bullet terminal | Female bullet terminal | Male bullet terminal | Female bullet terminal | insulation sleeve | insulation sleeve |
Tin-plating (gloss) | 24K plating (gold plating) | ||||
B-1 | B-2 | B-1-24K | B-2-24K | B-3 | B-4 |
Step 2: Cutting wire when old terminal is still attached
The crimping tool is equipped with a cutter to cut the wire, so you can work without nippers or other tools.
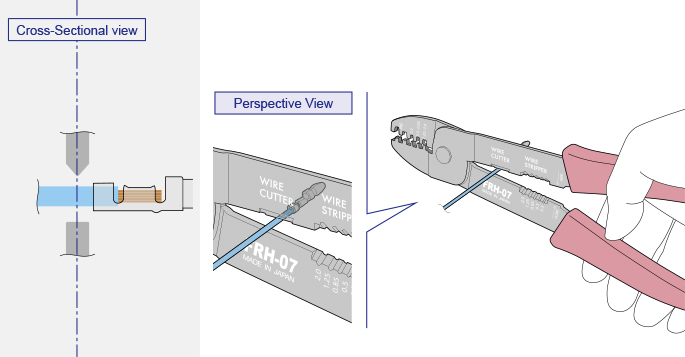
Step 3: Pass the insulation sleeve through the electric wire.
If the terminal is attached first, the sleeve will not be able to pass through, so the insulation sleeve should be passed through first. (In this manual, the male terminal is crimped at first, but you may crimp the female terminal first.)
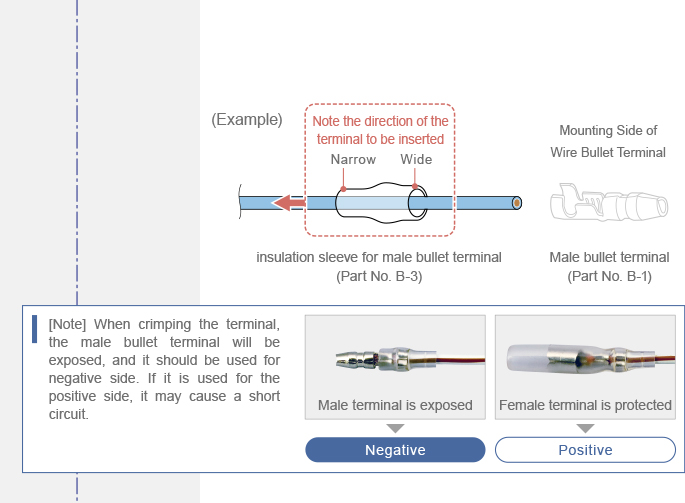
Step 4: Peeling off the INS (wire insulation)
Select the teeth according to the thickness of the core wire. The length of the INS (wire insulation) to strip should be about 1 mm longer (4-5 mm) than the crimped part of the terminal.
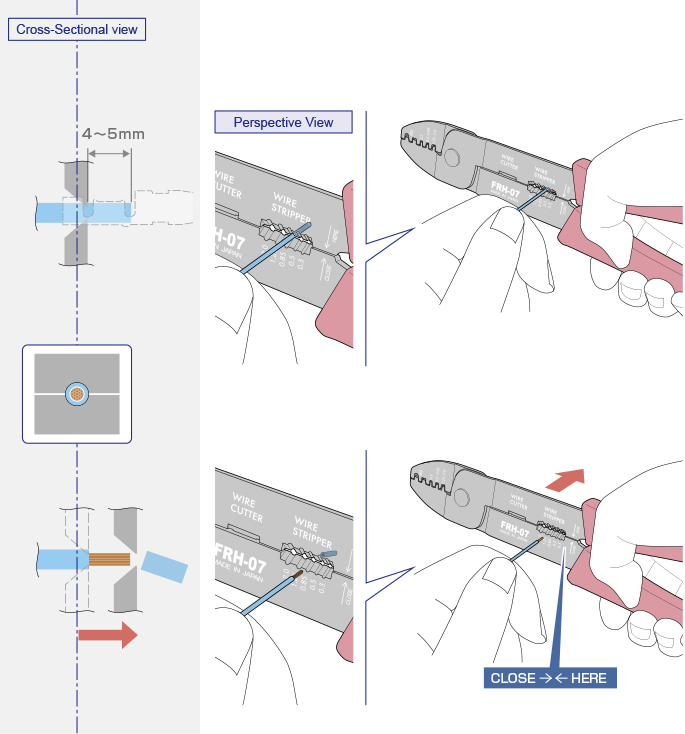
Step 5: Crimping the core wire of the electric wire (1)
Lightly pinch and fix the center of the wire core crimping part of the wire bullet terminal (Part No. B-1), and insert the wire into the wire core crimping part.
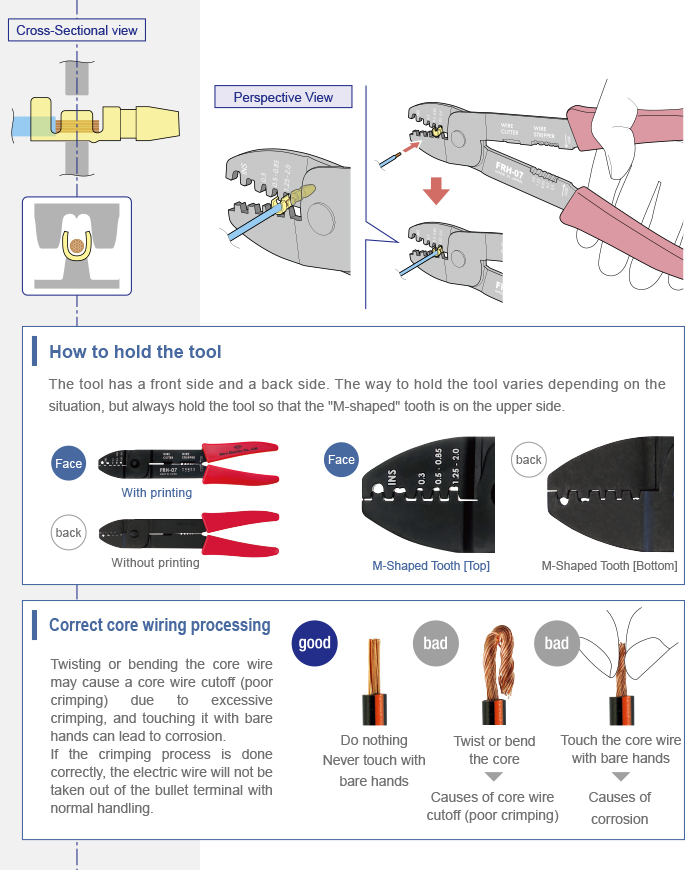
Step 6: Crimping the core wire of the electric wire (2)
Crimp the core wire by grasping the tool tightly until "CLOSE→←HERE" is closed.
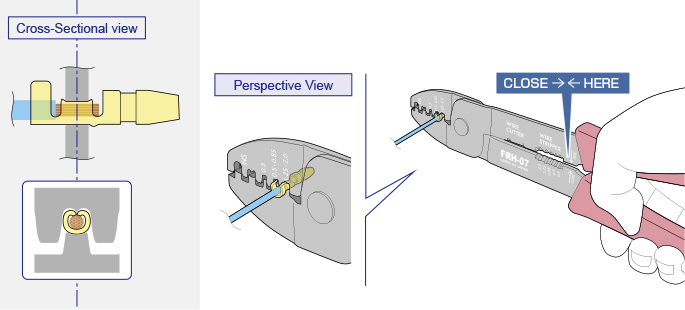
Step 7: Crimping the INS (wire insulation)
Crimp the INS (wire insulation) by placing it between the crimping teeth.
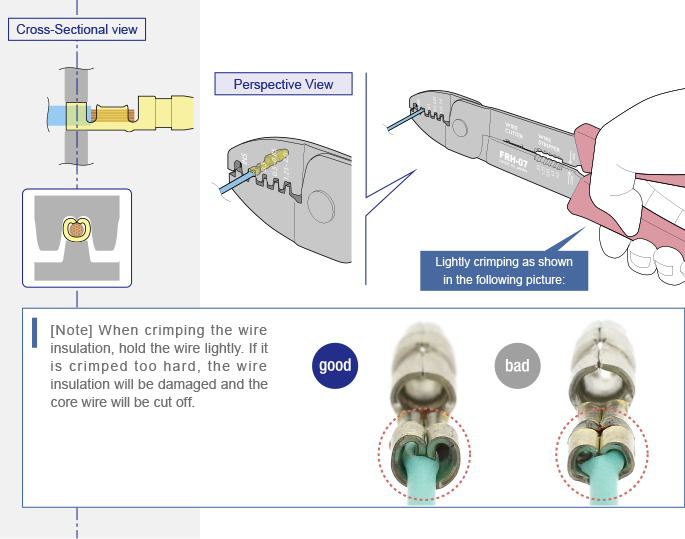
Step 8: Checking the finish and placing the insulation sleeve in a position
Insert the insulation sleeve into the terminal side. Make sure that the wire insulation crimped part of the terminal has been placed in the specified position for the insulation sleeve as shown in the following figure:

Crimping Tool "FRH-07" Two Types of Tooth shapes in the Wire Insulation Part
When crimping the insulation presser of the terminal onto the wire insulation, use the "M-shaped" tooth profile for the insulating part.
When crimping a waterproof rubber plug (wire seal), use the "round-type" tooth profile for the insulating part.
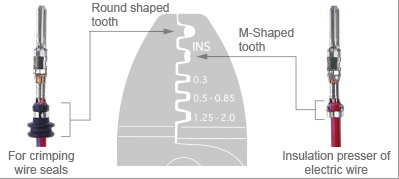